FMEA stand for Failure mode & effect analysis, it is a tool which is used for failure analysis in process and in design. Here we have covered AIAG+VDA FMEA is latest version of FMEA. In addition, this FMEA is proactive approach to solve problem come during project or production facilities. There are two types of FMEA.
- DFMEA- Design failure & effect analysis
- PFMEA- Process failure mode & effect analysis
Here only discussion is about FPMEA.
What is PFMEA?
PFMEA stand for process failure mode & effect analysis, method to identified potential failure mode in process & effect of those failure mode. It is risk management tool.
PFMEA is a team oriented systematic, qualitative, analytical method to evaluate potential risk of failure of process. With this we analyze the cause & effect of those failures, document preventive & detection action. Recommend action to reduce risk. In PFMEA we Analyse technical risk to reduce failure and improve safety in product & process.
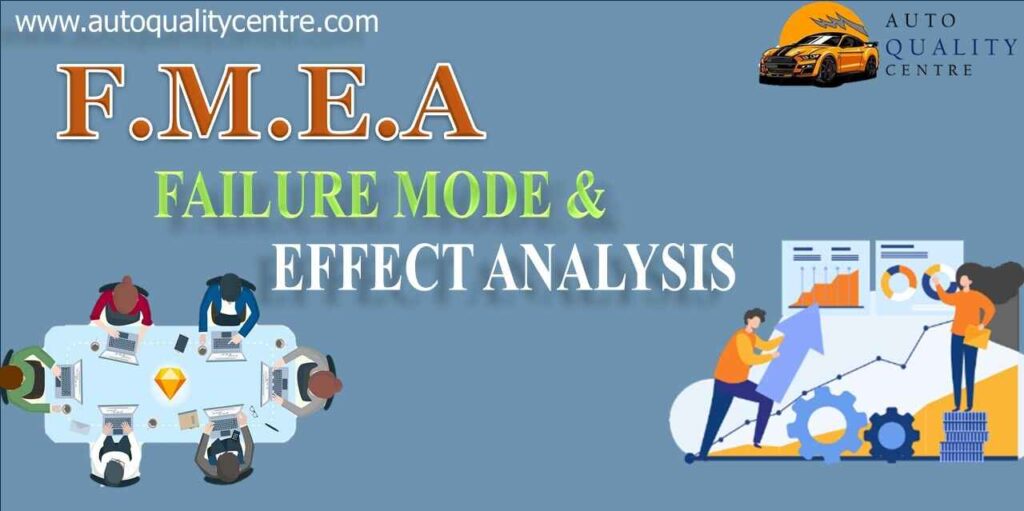
Background of AIAG+VDA FMEA
FMEA was developed by US aerospace & military sector in 1940. By 1960 FMEA was adopted by automotive industries as a tool to analyze potential failure modes in components, system & manufacturing process. Also this methodology was adopted by healthcare, electronics, software industries. By 1990 FMEA was integrated with Quality management system- TQM & Six sigma. AIAG added it as copyright standard & published various edition. Latest revision is AIAG- VDA 5th edition published in 2019. The new AIAG-VDA FMEA handbook was released in June 2019. Automotive Industry Action Group (AIAG) and Verband der Automobilindustrie (VDA), Germany’s associations for automotive manufacturers and suppliers issued the first edition of a joint FMEA book.
Why PFMEA is used?
With PFMEA we identify function of process steps, associate potential failure modes, effect of those failure mode, cause & control of those failure in process. This FMEA Also recommends additional action required to reduce potential risk. PFMEA is joint activity done with CFT, in which we do brainstorming to identify failure modes. It is qualitative approach with single point failure analysis.
FMEA is meant to be a “before-the-event” action, not an “after-the-fact” exercise.
What are benefits of PFMEA?
FMEA is joint activity between customer & their business partners, with PFMEA we try to find maximum failure effects and severity & reducing risk by analyzing over those technical risk.
Direct improvement can be seen in followings: –
- Product safety will improve
- Product quality will improve
- Smooth production launch
- Regulatory compliance
- Inter department communication
- Customer Satisfaction
When we need to do FMEA?
- When there is new technology, new design & development & new process.
- When there are changes in existing design & process like- Change in location, Engineering change in Existing design.
Changes in latest AIAG+VDA FMEA
Major changes are in format. Some new item added in new FMEA. Changes are as followed: –
- For continuous improvement, issue & revision history added
- Structure analysis is new addition. Process divided into process item, process step & process work element
- Functional analysis is expanded according to function of focus element, function of process step & work element.
- Failure analysis- No change
- Risk analysis (Occurrence control / Detection control)- RPN replaced by Action Priority
- In Optimization, Recommended action divided by Prevention action & detection action, also status column are added
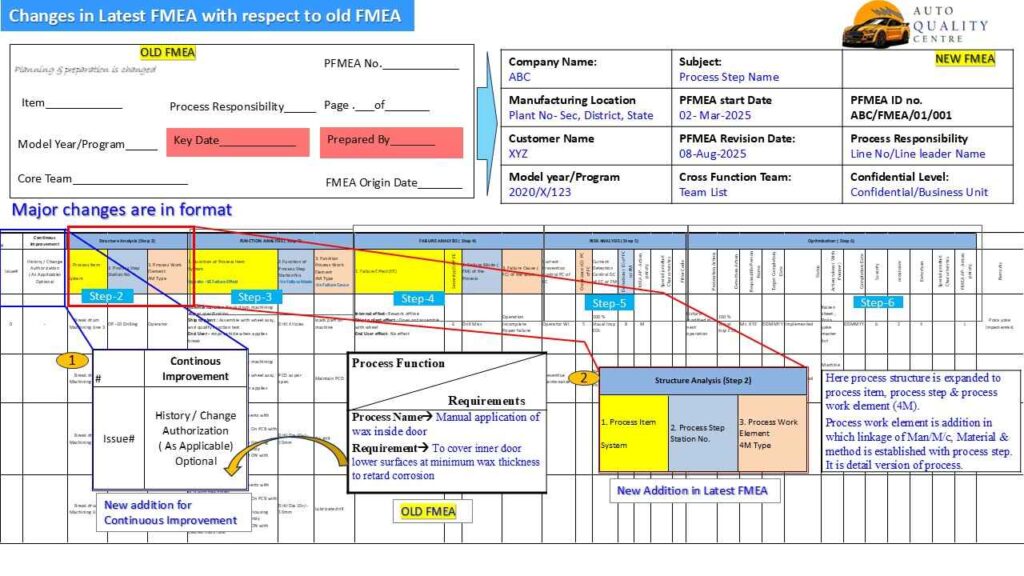
Methodology of AIAG+VDA FMEA?
Latest FMEA is based on 7 step implementation process. This FMEA is divided in 7 steps which provide systematic approach for failure mode analysis & risk mitigation.
7 steps are as followed: –
- Planning & Preparation
- Structure Analysis
- Functional Analysis
- Failure Analysis
- Risk analysis
- Optimization
- Result documentation
Here first 3 are related to system analysis while 4 to 6 are related to failure analysis & risk analysis. Finally, Step7 is basically risk communication.
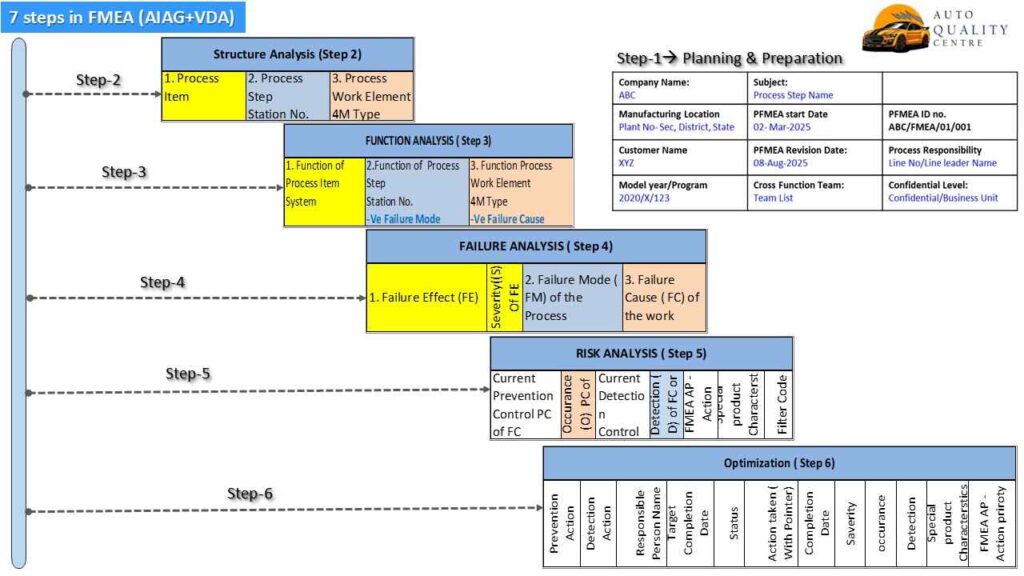
FMEA The purpose of the Failure Analysis Step is to identify failure modes; failure effects and failure causes to establish the basis for the risk assessment. Objective is to establish failure chain. Identifying potential failure effect, failure mode & failure causes of each process function.
FMEA Step 1- Planning & Preparation
It is clear definition of the scope, set by the management team. Planning is done based on Five T’s. Information from this step is basis for step-2. So, this is very important step of FMEA.
Purpose: – To describe what product /processes are to be included for review in the PFMEA Project. During planning & preparation objective is to project plan, consideration of analysis boundaries, project identification for this following information need to collect.
- What are customer expectations (Internal & External).
- Technical requirements
- Drawings & specifications
- BOM & Risk assessment
- Error proofing requirements
- QFD – Quality function deployment (CFT)
FMEA Step 2- Structure analysis
This step is used to identify and breakdown the system (Design or Process) into the system, subsystems and component element so that a comprehensive risk assessment can be conducted. This information is the basis for the next step.
Purpose: – to identify and breakdown the manufacturing system into process items, process steps and process work elements. Objective of this step is to make structure tree of process, identification of process step & sub steps, to be base for function analysis.
Process item is highest level of integration within the scope of analysis. It is result of all of successfully completed process step.
Process step is topic of consideration of failure chain & a focus element. It is manufacturing operation & station.
Process work element is next level down from focus element. Related to 4M change. It contain potential cause of failure.
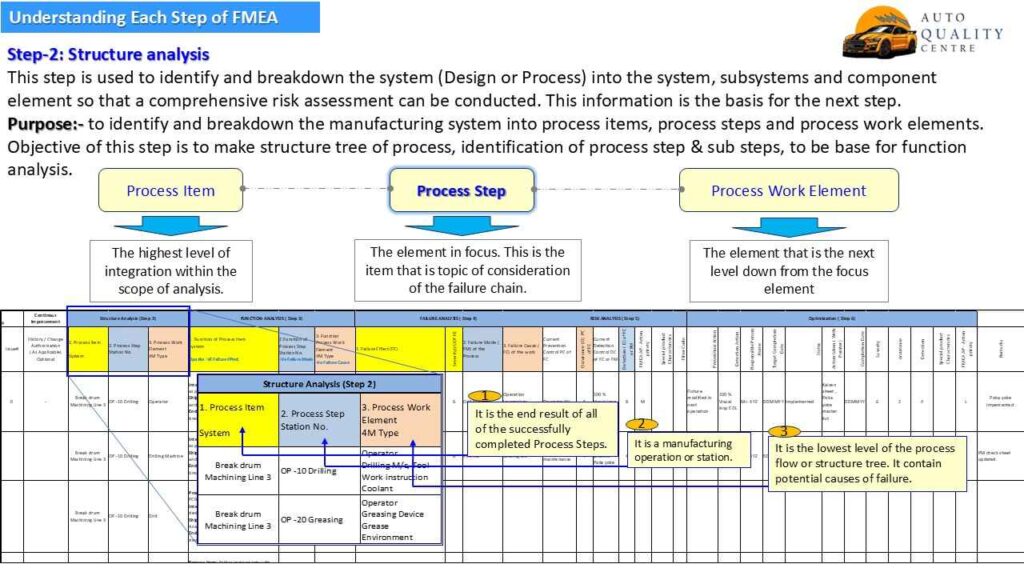
FMEA Step 3- Functional Analysis
This step is used to analysis of indented function & requirements of system element identified in step-2. Objective is to visualization of product & process functions. Finding requirement & characteristic of functions. This will become base for Failure analysis.
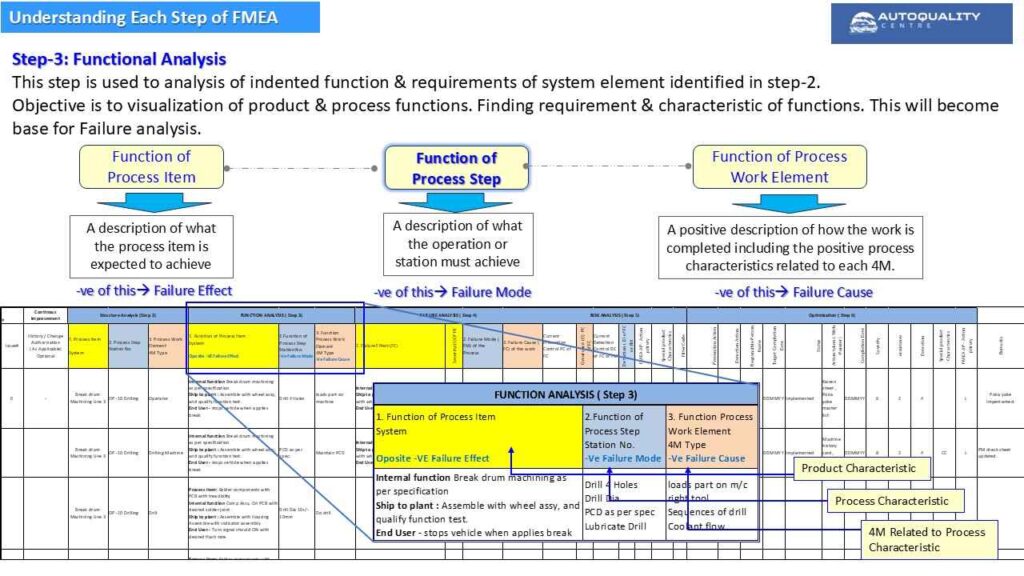
Function of process item- A description of what the process item is expected to achieve. Negative of this will be failure effect. It is product characteristics.
Function of process step- A description of what the operation or station must achieve. It is process characteristic, and negative of this will be failure mode.
Function of process work element- A positive description of how the work is completed including the positive process characteristic related to each 4M. Negative of this will be failure cause.
FMEA Step 4 – Failure Analysis
The purpose of the Failure Analysis Step is to identify failure modes, failure effects and failure causes to establish the basis for the risk assessment. Objective is to establish failure chain. Identifying potential failure effect, failure mode & failure causes of each process function.

Failure effect- It is related to function of process item, negative of it will be Failure effect. It talks about What happen?
Failure mode- It is related to function of process step, negative of it will be Failure Mode. It is focus element here. Failure mode will give failure effect & failure cause, so first work on failure mode.
Failure cause- It is related to function of process work element, negative of it will be Failure cause.
FMEA Step 5 – Risk Analysis
The purpose of the risk analysis is to estimate risk by evaluating severity, occurrence and detection, in order to prioritize the need for actions. Objective is to Evaluation of Action Priority after assignment of detection control & prevention control of failure causes. This becomes bases for optimization step.
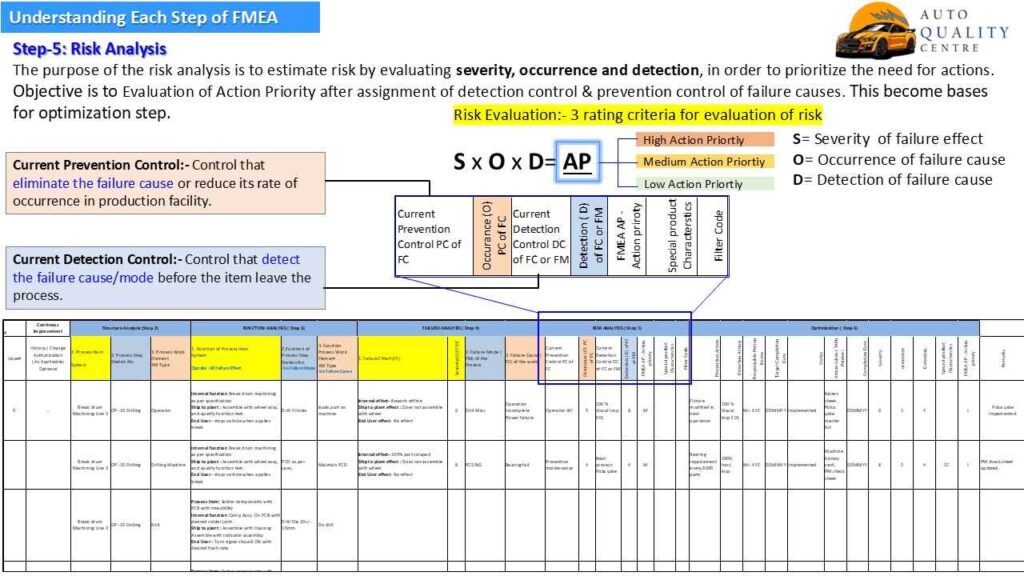
Current Prevention Control: – Control that eliminate the failure cause or reduce its rate of occurrence in production facility.
Current Detection Control: – Control that detect the failure cause/mode before the item leave the process.
Risk evaluation is done based on 3 rating criteria of evaluation of risk. 3 rating are given for Severity (S), Occurrence(O) & Detection(D). Multiplication of 3 will be Action priority (AP). Further action priority is classified into 3 more categories: – 1. High action priority, 2. Medium action priority & 3. Low action priority.
Action Priority:
- High Action Priority:- The team must identify an appropriate action to improve prevention and or detection control or justify and document why current controls are adequate.
- Medium Action Priority:- The team should identify an appropriate action to improve prevention and or detection control or justify and document why current controls are adequate.
- Low Action Priority:- The team could identify an appropriate action to improve prevention and or detection control.
FMEA Step 6 – Optimization
It is the step where plans (Preventive & detection plans) are developed that reduce risk and increase customer satisfaction by improving the design or process. Objective is To identified actions to reduce risk, assign responsibility, deadline, base for refinement of product/process requirements. (At a minimum the statement that “No further action is needed” must be included)
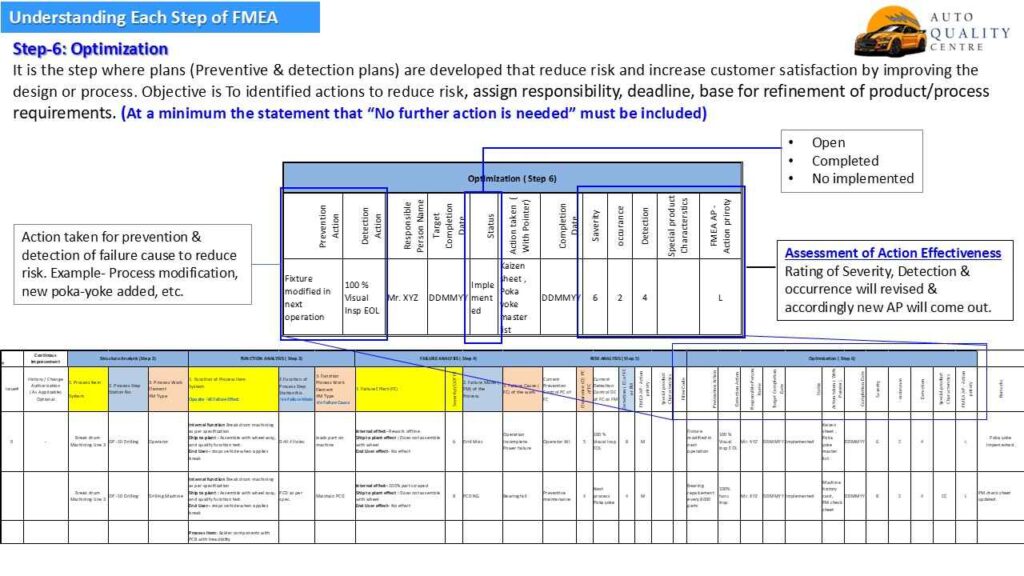
Prevention & detection control column talks about- Action taken for prevention & detection of failure cause to reduce risk. Example- Process modification, new poka-yoke added, etc. Status of FMEA could be Open / Implemented / No implemented.
Assessment of Action Effectiveness– Rating of Severity, Detection & occurrence will revised & accordingly new AP will come out.
FMEA Step 7- Result Documentation
This is final step; here we documented the FMEA study. The results of the FMEA investigation should be summarized in a report. The report should be to communicate the results throughout the organization
The results need to show the success & relevance of the analysis. It has to be presented in specific format.
Read 2 min post on Cause & effect analysis
Pingback: Basic Know How of Multimeter device - AQC
Pingback: Poka Yoke Types and its basic Function - AQC